In the world of robotic dairy farming, where every minute counts and every cow’s well-being is paramount, ensuring the smooth operation of robotic systems is more than just a priority—it’s a necessity. At Lely Center Mid-Atlantic, we understand the critical role maintenance plays in achieving optimal performance, efficiency, and, ultimately, profitability for our customers. That’s why in 2023, we made a commitment to prioritize maintenance like never before.
Embracing Lely’s recommended 4x/year maintenance schedule, we standardized our protocols to ensure consistency across every service visit, regardless of the technician performing it. We meticulously reviewed key components on each model of robot, identified high-failure parts, and integrated their maintenance into our protocols. This proactive approach was especially crucial considering the average age of robots in our dealership, which stands at nine years old.
The impact of our efforts was tangible and impressive. In 2022, we performed 80 maintenances and received 81 emergency calls. However, in 2023, despite an increase of six more robotic farms and 18 additional robots, we completed 138 maintenances, and we saw a decrease in emergency calls to 75. The most notable change was the significant decrease in preventable calls due to maintenance parts failing, indicating a clear correlation between diligent maintenance and reduced downtime.
Our ultimate goal, mirroring Lely’s vision, is to achieve 100% uptime for our customers. This isn’t merely an aspirational target; it’s a commitment to predictability, service efficiency, safety (for both cows and humans), performance, and cost-effectiveness. Since overhauling our maintenance protocols, we’ve witnessed a remarkable improvement in the consistency of our robotic “herd’s” uptime, with an average around 99.3%.
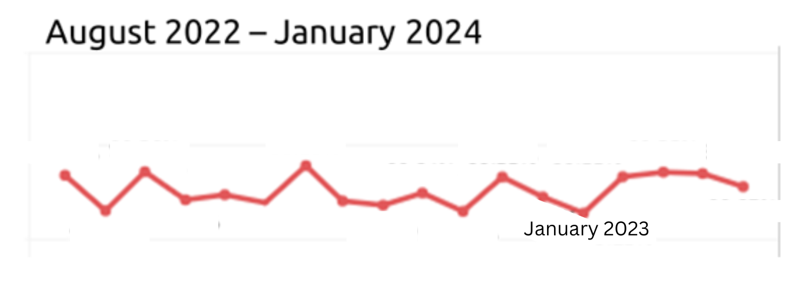
To underscore the importance of maintenance, let’s examine a case study (see image below): two farms that adhere to regular maintenance schedules versus two that do not. The contrast is stark. The latter experience 2.2 and 0.7 hours of downtime due to critical alarms per day, equivalent to 66.73 and 21.23 days of preventable downtime per year, respectively. In contrast, the former enjoy 99.91% uptime, translating to a mere 1.3 days of preventable downtime annually. The math speaks for itself—maintenance pays dividends.
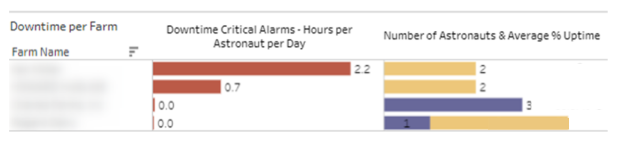
It’s worth noting that critical alarms per machine per month across North America are still prevalent, but with diligent maintenance, their impact can be mitigated. Astronaut A3, A4, and A5 models experience an average of 6.1, 6.4, and 5.4 critical alarms per month, respectively.
In summary, we recognize the immense value of uptime to our customers, the efficiency of Lely Center, and the well-being of our service technicians. As we stride into 2024, we remain committed to refining our maintenance protocols to deliver the superior quality of service our customers expect and deserve. Maintenance isn’t just a task—it’s the backbone of reliability, efficiency, and success in the modern dairy industry.